Initial fill services
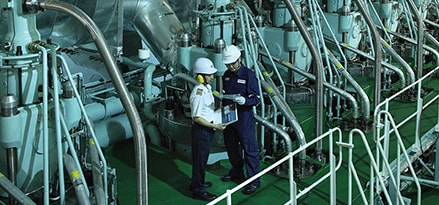
Identifying initial fill steps and coordinating lubricant delivery can help reduce your operational, maintenance and labor costs while boosting your plant’s productivity.
Description
New equipment installations can cause contamination in your lubricant circulation system, which can lead to high levels of costly wear. To help you avoid the expense of unplanned maintenance for equipment repair and replacement, experienced engineers offer on-site coordination of lubricant delivery and certify that the initial fill charge meets or exceeds original equipment manufacturer (OEM) specifications.
Application
Expert engineers will work with you to:
- Recommend the right lubricant for the application
- Establish oil cleanliness specifications consistent with OEM requirements
- Identify initial fill steps to help ensure optimal performance of the new equipment
- Coordinate new lubricant delivery
- Coordinate arrangements with the provider who will:
- Filter the lubricant, fill the system and certify lubricant cleanliness within acceptable levels prior to the machine becoming operational
- Gather key baseline and other relevant data
Deliverable:An Engineering Service Report details the lubricant treatment steps completed, documents the lubricant cleanliness level prior to and after treatment, recommends steps to maintain lubricant system cleanliness and provides an estimated value of the service. Distribute and present the completed report to plant management and key personnel.
Common opportunity areas
- New equipment commissioning
- Scheduled equipment outage
Safety, health and environment
Field engineers are attuned to the hazards of handling, storing and using petroleum products. They strictly observe safety and environmental rules and ExxonMobil and customer safety practices. They coordinate efforts through designated plant personnel verifying electrical and mechanical lockout and proper tagging prior to working on equipment, and providing recommendations to help reduce hazards.
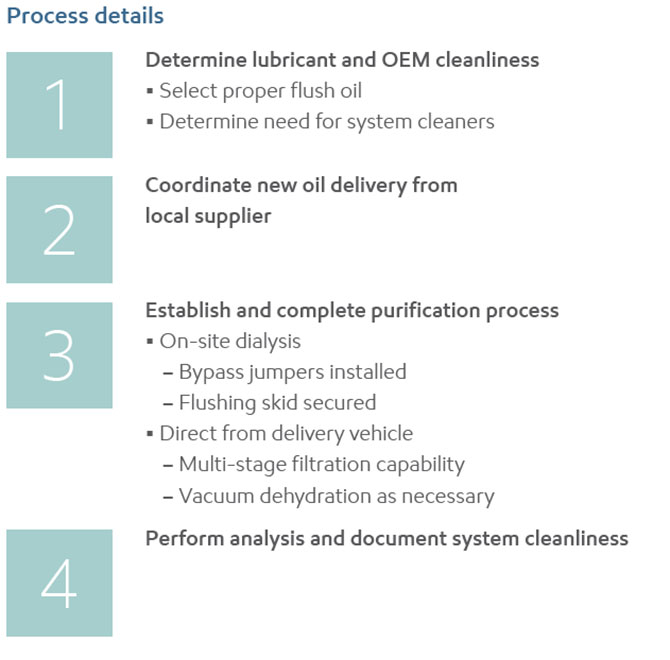
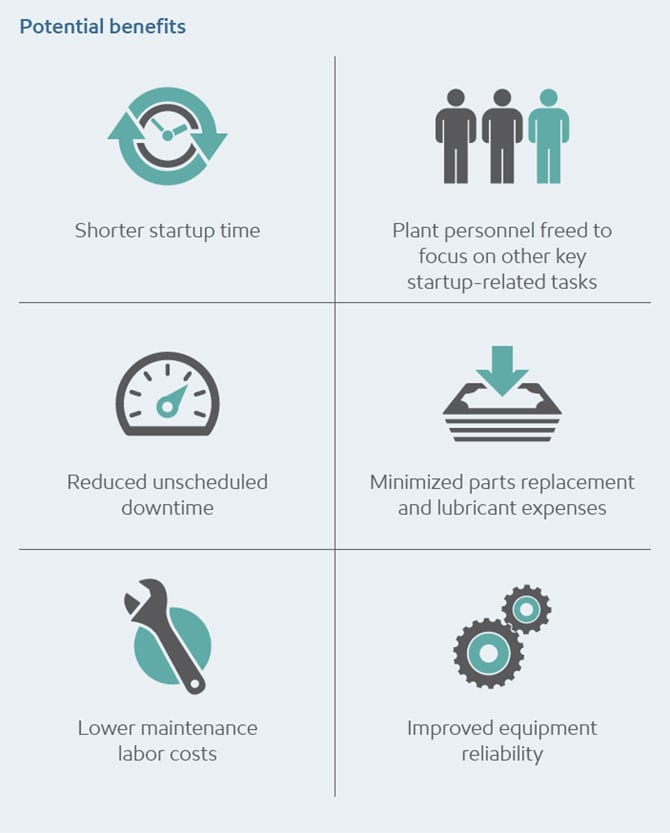